Recently, this house in the historic district of Grant Park, Atlanta, was certified through the ENERGY STAR New Homes program at the EPA. The final inspection revealed an air tightness of 0.77 ach50, which is near the maximum acceptable air infiltration level of the aggressive Passive House program (0.6 ach50). The final HERS Index was around 64, which means (among other things) that home should perform at least 36% better than a similar home built to meet the current energy code.
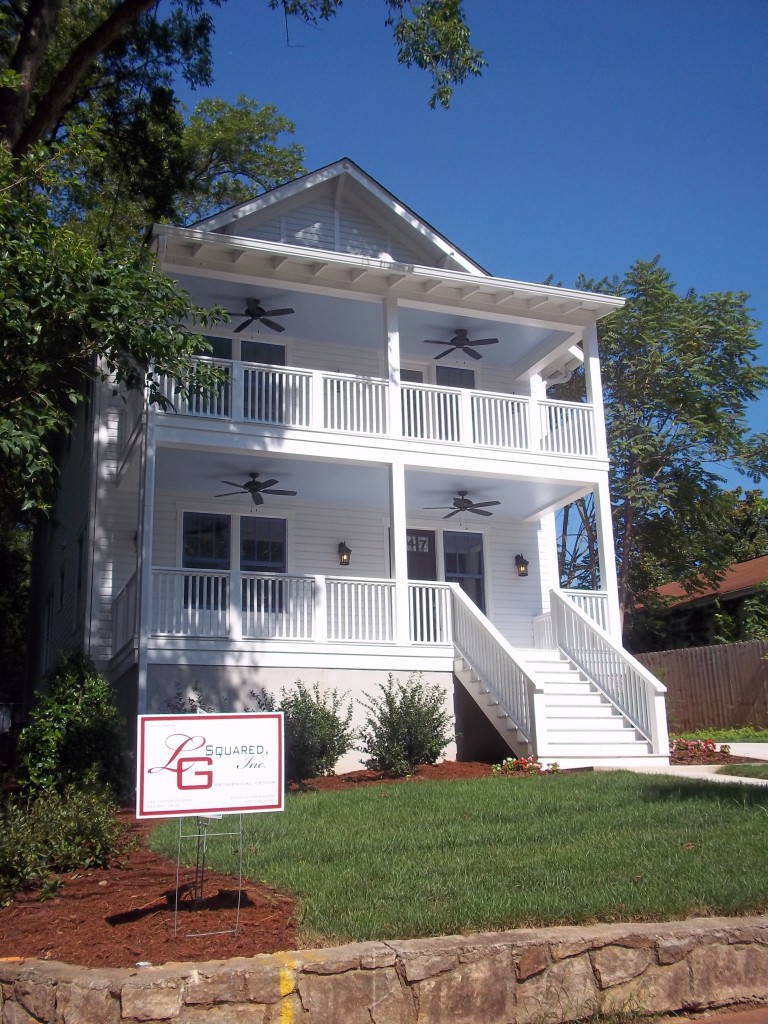
The home is 2,350 square feet with 4 bedroom and 3.5 baths. Ceiling heights are 10'-0" on the first floor, and 9'-0" on the second. It is built on an encapsulated crawlspace, and has an encapsulated attic where some of the HVAC equipment is.
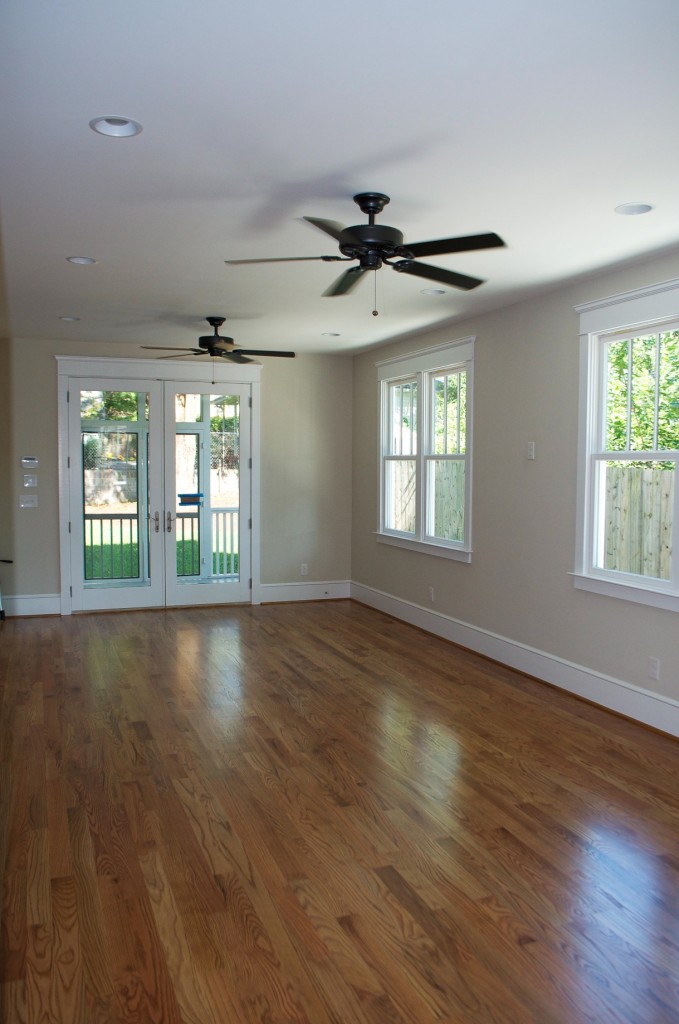
Oak floors throughout, and the custom stained glass featured in the home was made by the builder's mother.

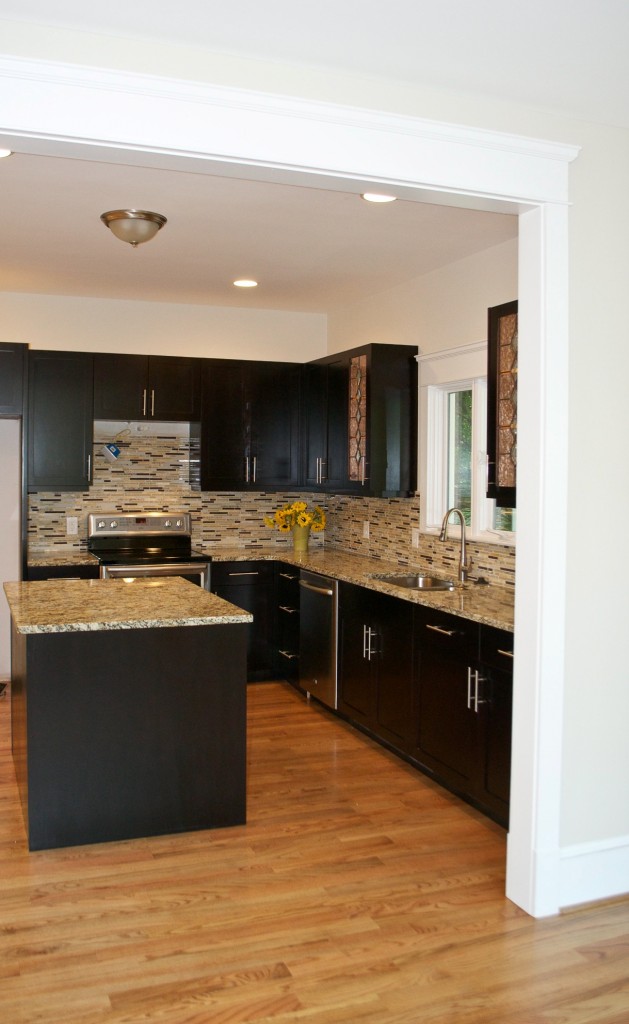
The construction drawings included critical air sealing, water management and thermal boundary details, energy models, heating and cooling load calculations and a complete HVAC design (ACCA: Manual J, Manual S and Manual D) that guided the builder and his sub-contractors to exceed the guidelines of the ENERGY STAR program. All of this was in addition to the standard drawings required for construction. It was one of the first Designed to Earn the ENERGY STAR projects that I completed, and a great example of how integrated design
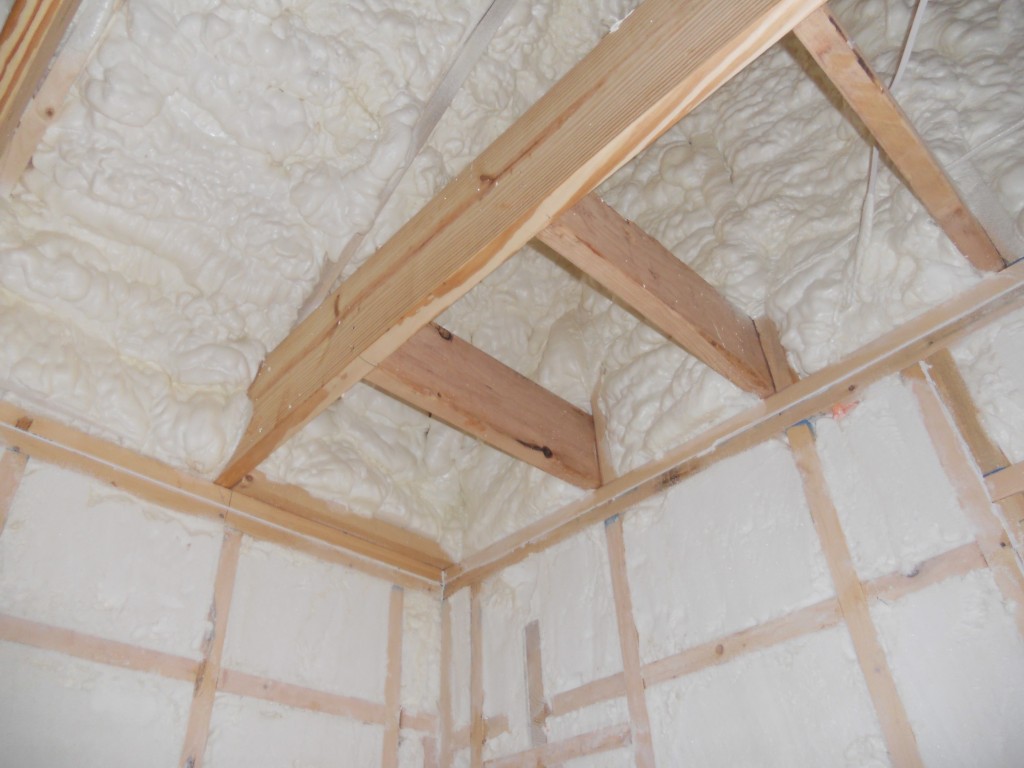
The entire building envelope, from the foundation to the peak of the roof, was filled with an open-cell spray foam insulation that contributed to both the thermal boundary and air barrier. All of the exterior wall (2x4) cavities were filled with the foam (R-13), and roof structure (2x6) was filled to provide a minimum R-20.
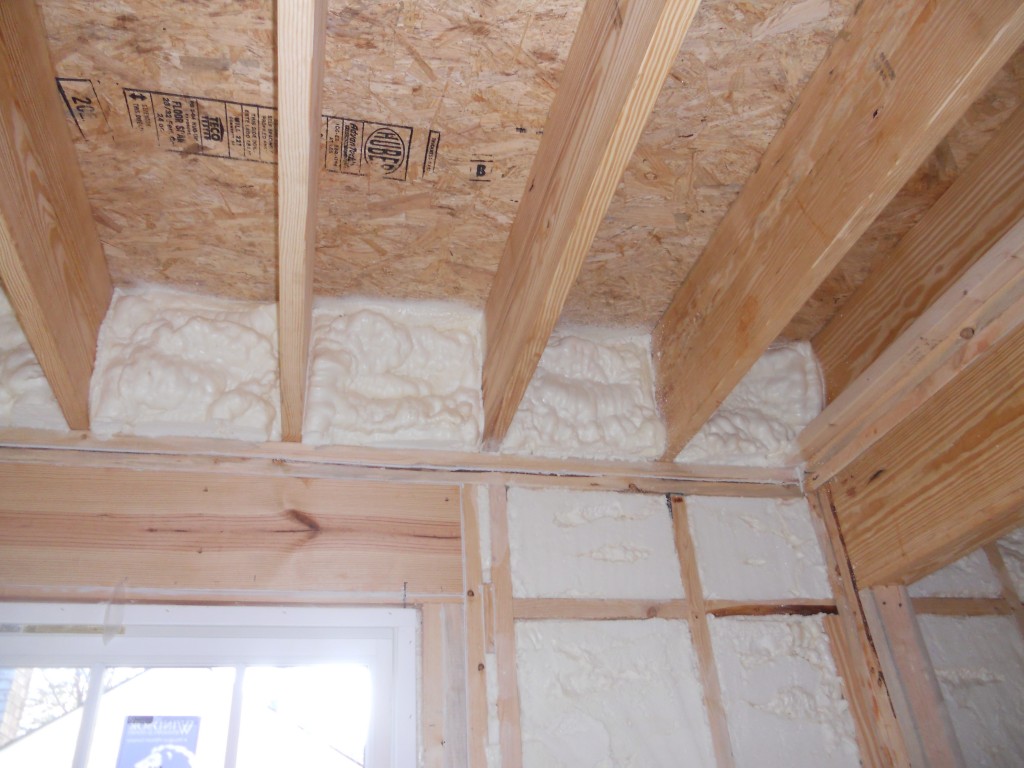
In multi-story framed homes, and those built on a crawl space or foundation, the band joist is a critical point where heat loss and infiltration (especially) can happen. Completely filling the cavities with the foam is one of the simplest ways to effectively control both.
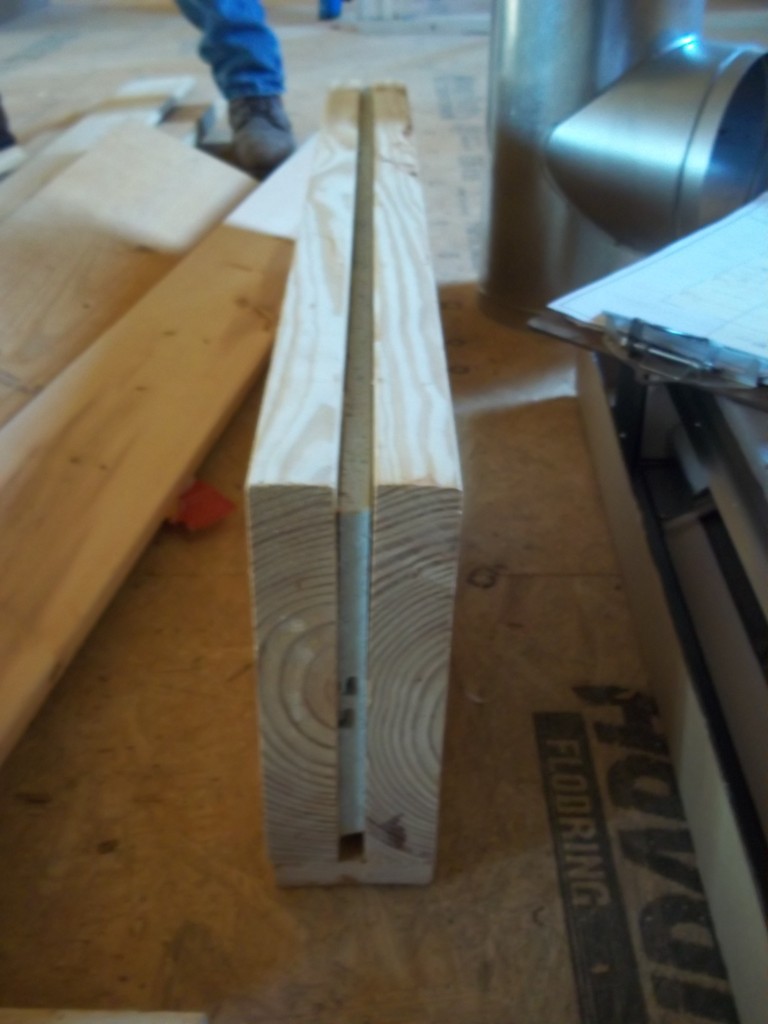
To minimize thermal bridging, details were provided for advanced framing techniques like this insulated header. The 1/2" layer of foam replaced what is normally a sheet of OSB sheathing or plywood. Below shows an opening in a load-bearing and non-load-bearing wall to show that it's not necessary to provide structural headers in every opening. It's common to find interior wall openings that have no load whatsoever built with 2x6, 2x8, or 2x10 structural headers, when simple cripple studs will do.
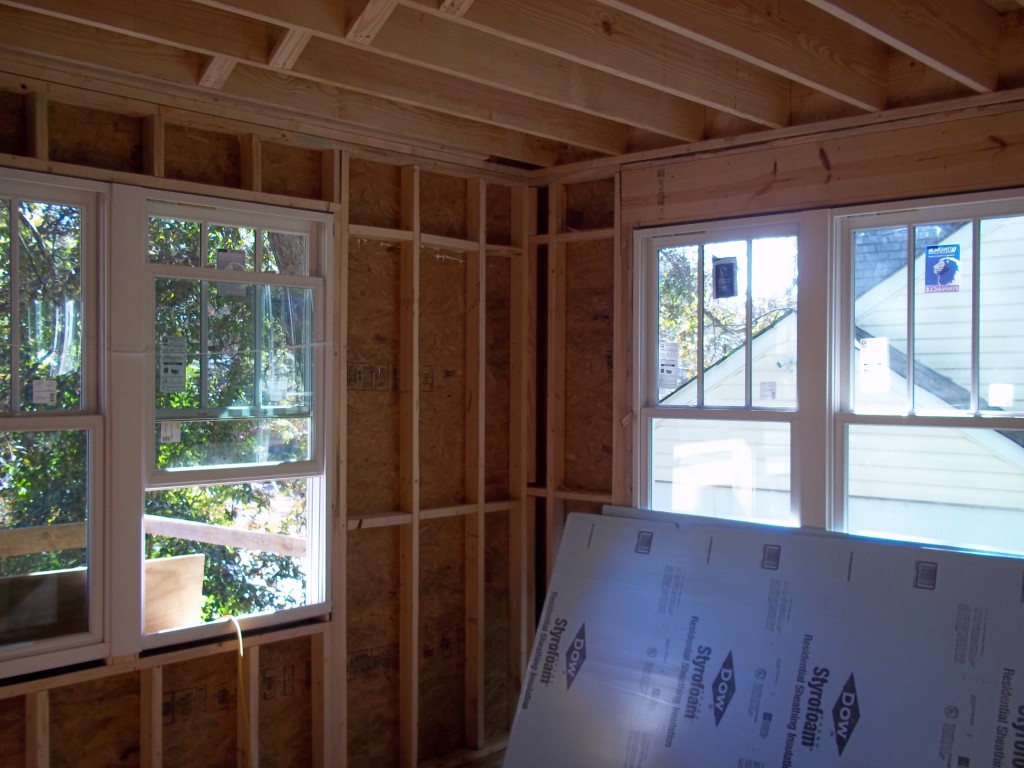
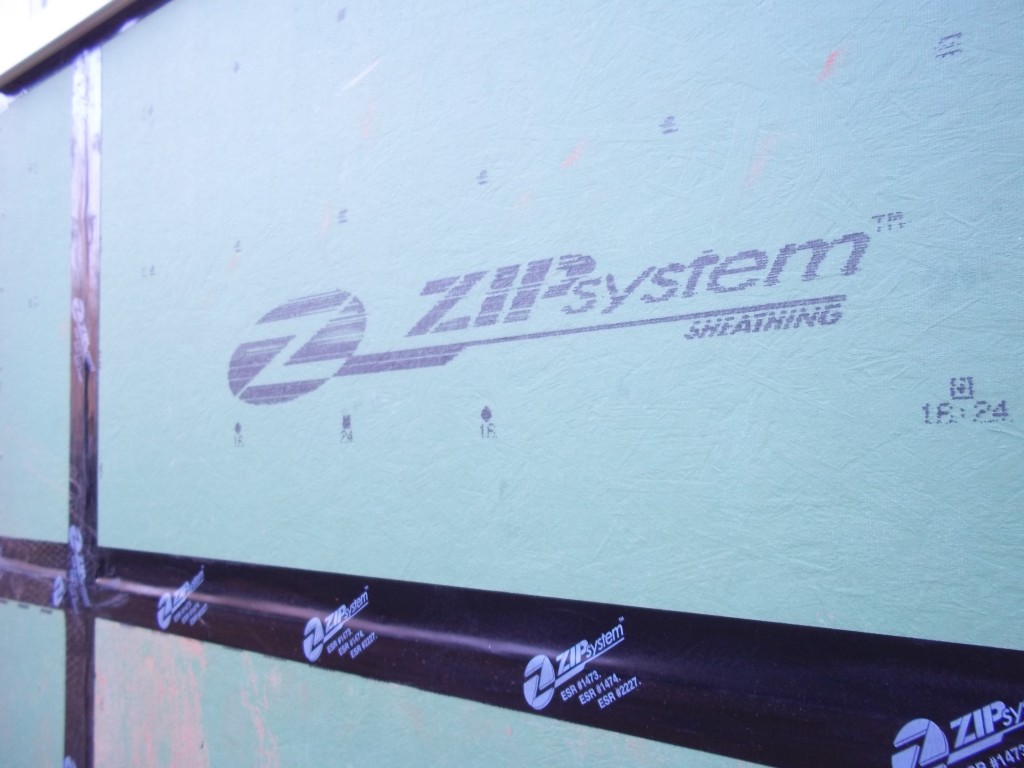
The ZIP System wall and roof sheathing, also available in a combo panel (shown here, for both roof and wall) was specified for the exterior sheathing (structural) because it has an integrated water resistive barrier (WRB, in lieu of house wrap). The WRB and the ZIP System tape also provide an air barrier in both directions (inward and outward) to decrease infiltration and exfiltration.
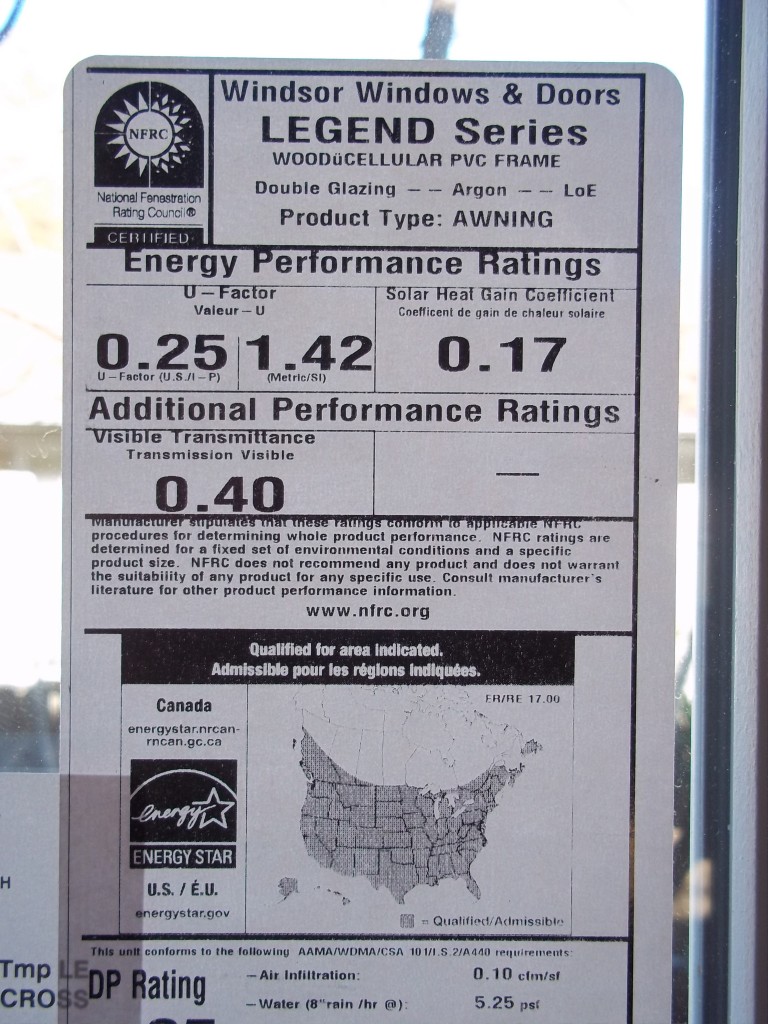
All windows were specified with a maximum U-value of 0.30 and SHGC (solar heat gain coefficient) of 0.25. As you can see, we were able to exceed these specs. In hot and warm climates like the one this house is in (Climate Zone 3), the SHGC has more of an impact on the heating and cooling loads of a home, especially on south, west and east facing walls.
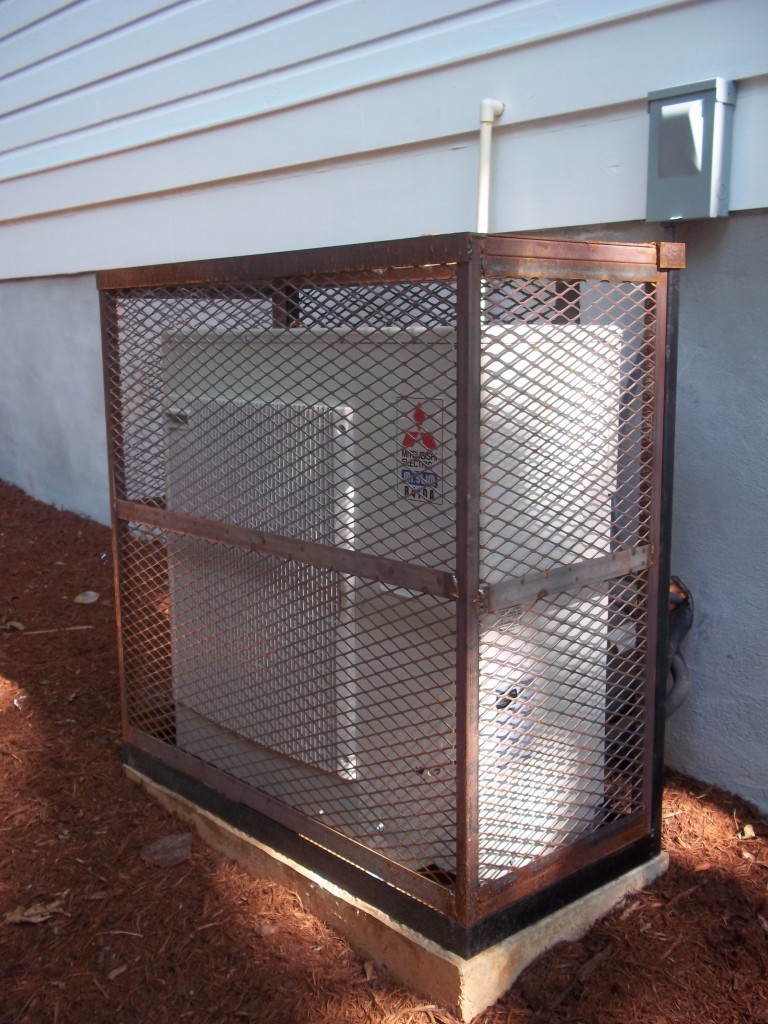
The heating and cooling load calculations for this home were very low. For the entire house (2,350 s.f.), the cooling load came out to less than 18,000 btu/h (approx. 1,650 s.f. per ton) and the heating load is 22,500 btu/h. I designed and specified a Mitsubishi Ducted Mini-Split Heat Pump System, with it's variable refrigerant flow technology, to handle the low loads and dehumidification. There's one ducted unit (seen below) serving the first floor and one serving the second floor.
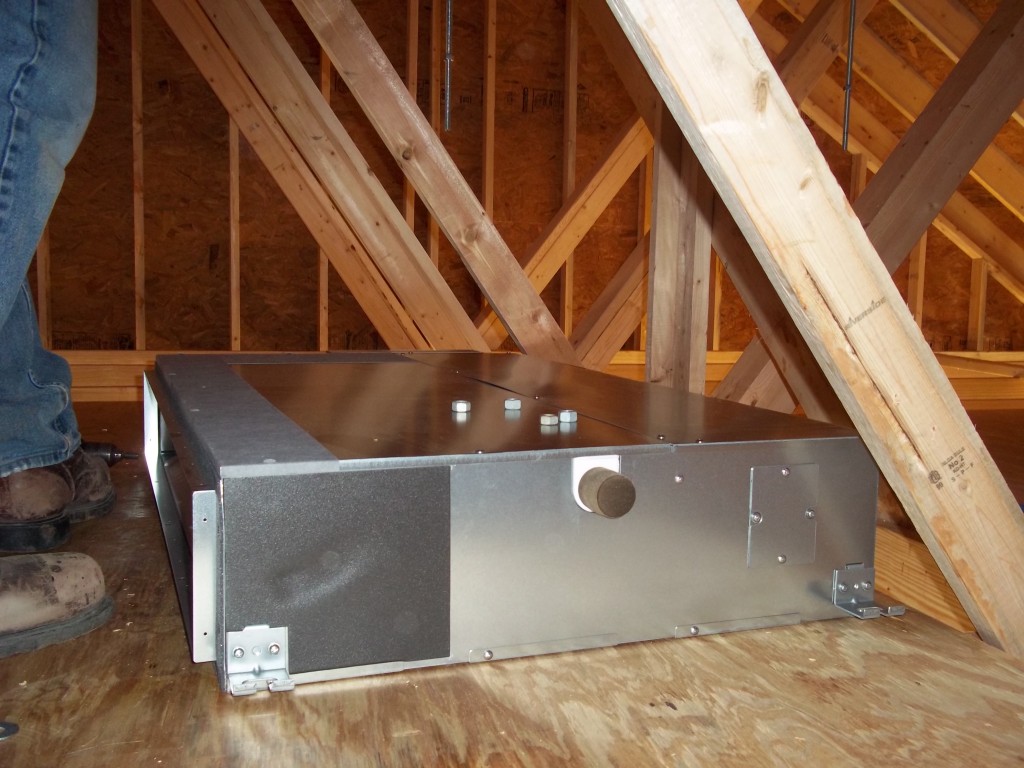
The projected energy bills for this home are in the range of $50-$75 per month, depending on occupant behavior and the utility rates at that time. This low usage is due in large part to the low loads, efficiency of HVAC system, the compact fluorescent light bulbs, and the efficient appliances installed in the home.
A couple other features (there are many more) that helped the home perform well and to certify as ENERGY STAR were:
- Energy (or Enthalpy) Recovery Ventilator - provides fresh air to the home while recovering some of the heat energy from the return air to pre-condition the fresh air coming in to the home.
- Continuous foundation drain at the perimeter of the concrete footing to help prevent water from entering the home through the foundation. The foundation walls were also treated with a dampprofing.
...