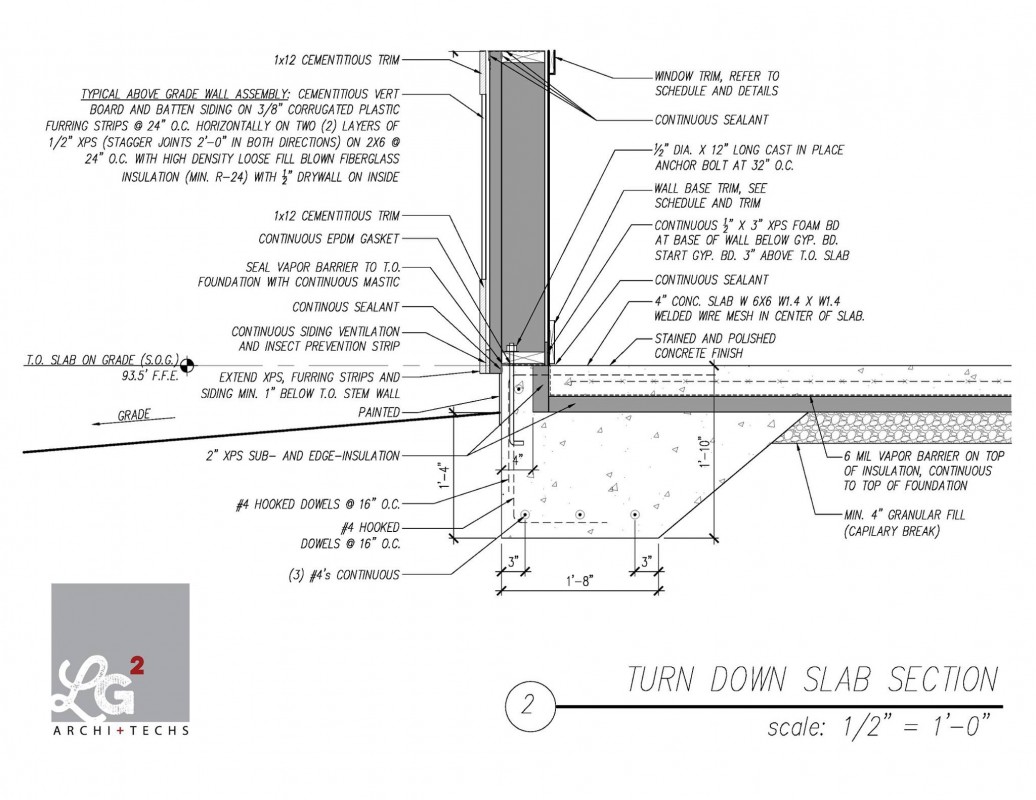
Thousands of hours went in this construction detail. When we factor all the time spent by building science engineers, from all over the world, researching and testing each material and the various assembly options, and to figure out what works and what fails, the time is, really, impossible to quantify. Not to mention the time we spent researching, testing, making decisions, designing, and drawing this detail, for this specific project? Our time, of course, was just a blink of an eye, in comparison.
Then, there's the time that goes in to educating consultants, sub-contractors, homeowners, and sometimes even building inspectors, about the importance, and the results, of integrating building science best practices in to the architectural and interior design, as well as the construction or remodeling of a home. To name just a few of the targeted results:
- Nice, appealing places to live that last a really long time, that are durable, and don't fail;
- Homes that don't kill their occupants, or make them sick. Controlling air quality matters;
- A lot less energy consumption. This means more money in the bank for the homeowner, and, for many, there's a feel-good benefit about contributing to a global cause, that some call a "crisis";
- Comfort. Without it, people get cranky, and either they stay cranky and become "that" neighbor, or they find a better place to live. Either way, it's a shame...and wasteful. For those that chose to stay cranky, Ralph Waldo Emerson had some advice, "For every minute you are angry, you lose sixty seconds of happiness." Don't waste happiness.
Without a good understanding, no, knowledge of material and building science, architects, builders and tradespeople put homes at risk of early failure. But, is it enough to simply know material and building science to achieve a long lasting, high performance home?
...Unless it is Well Executed
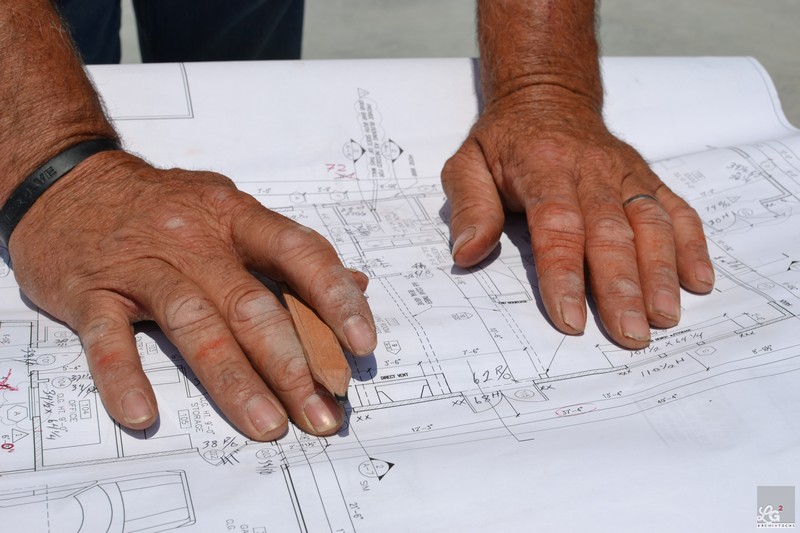
Building Science might as well not exist, without proper, no, perfect execution. In the same way that we need it for dovetailing cabinetry, or the perfect mitered corner, the only way to make the science work, and to achieve high performance, is to execute it with good Craftsmanship. Period!
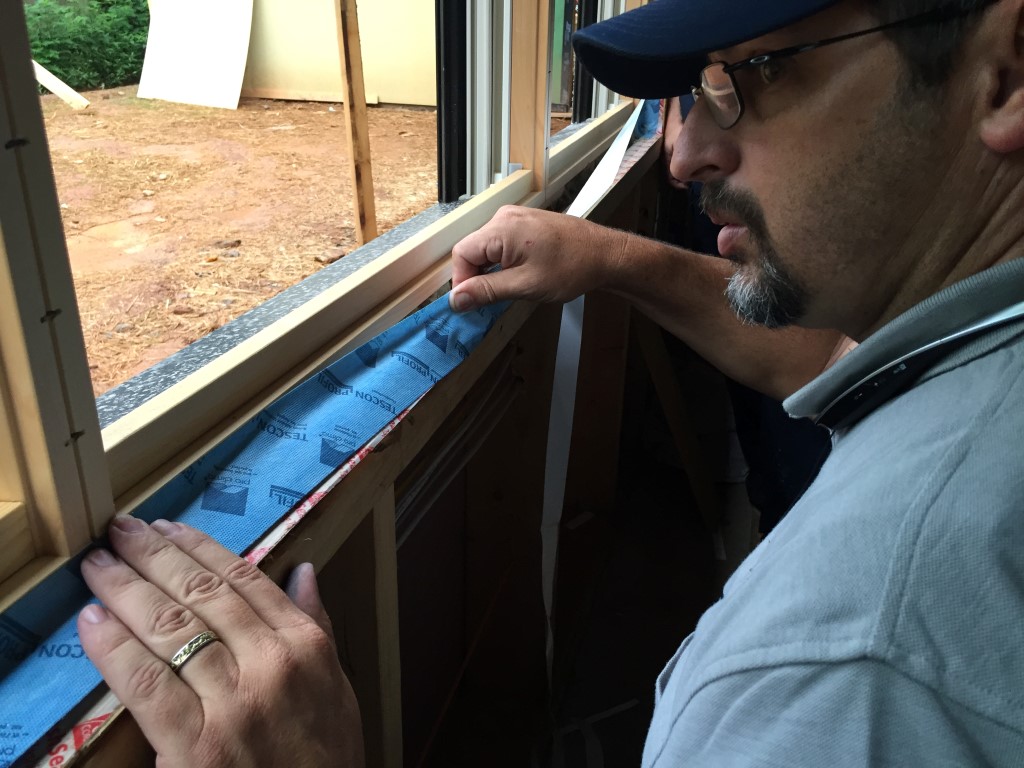
When LG Squared takes on the role of builder and architect of high performance homes, the Modus Operandi that we repeat to every one of the tradespeople is, "Do It Right". This means different things for each project, so, what is "right" must be reviewed, for each home. It's also important that everyone sees "Do It Right" as an opportunity, rather than a challenge.
Our pal, and fellow builder and building science geek, Matt Risinger, of Austin, TX., knows a thing or two about building science and fine craftsmanship, and would, no doubt, concur that execution is our greatest opportunity.Here's what he has to say: https://www.youtube.com/user/MattRisinger
On the High Performance Bungalow project, in Roswell, Georgia, there were many "opportunities". One of our favorite opportunity moments was during the installation of the second of two continuous layers of exterior rigid foam, when we received this text from our installer...
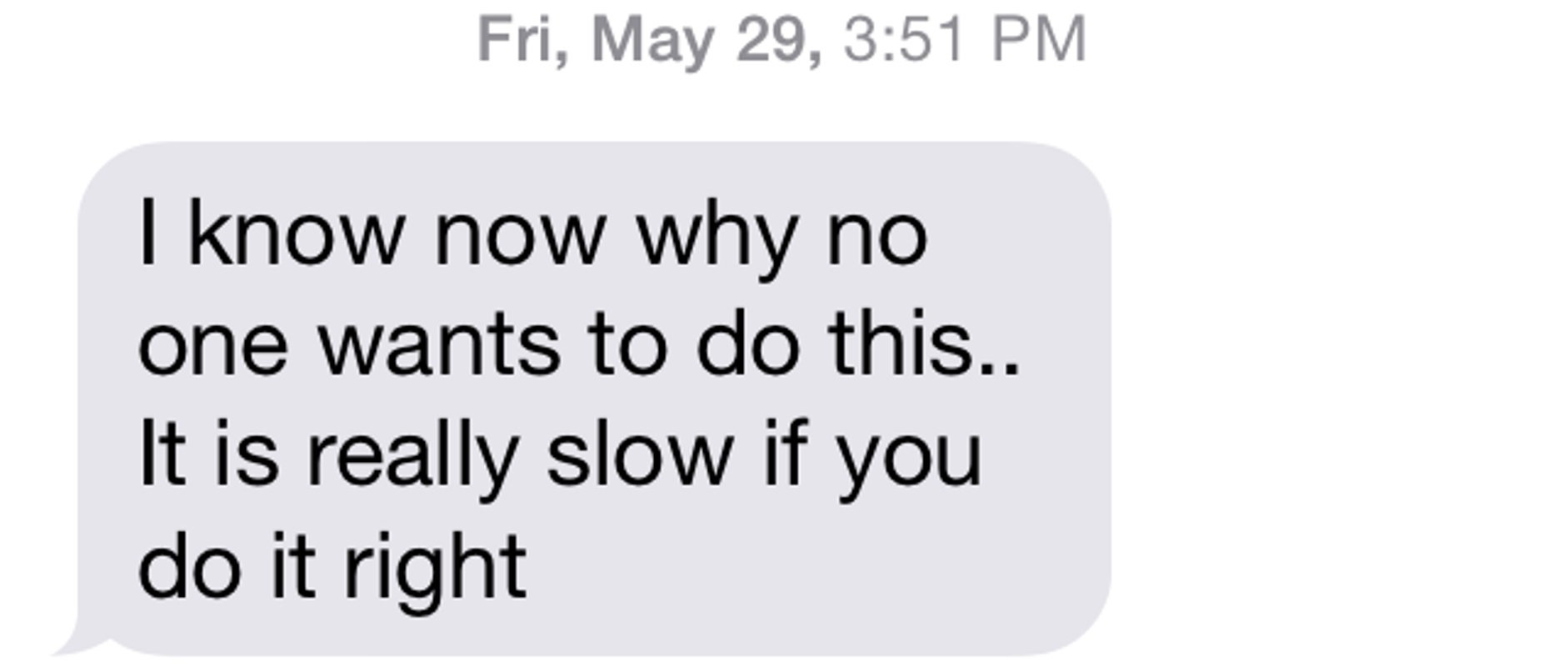
The building science says that, for the two layers of XPS (extruded polystyrene) to perform at their best, they should: 1. Be installed so that the seams, where two 4x8 sheet come together, are staggered from one layer to the next; 2. Seal every one of these seams, and all edges, on the outer layer, to make continuous the weather resistive and air barriers; and, 3. Use only a certain thickness of that type of foam, based on interior and exterior climate conditions AND how the rest of the assembly is built. Getting the first two right, is up to the crafts-person, the installer. Getting the last item right, is up to us, the science and design people.
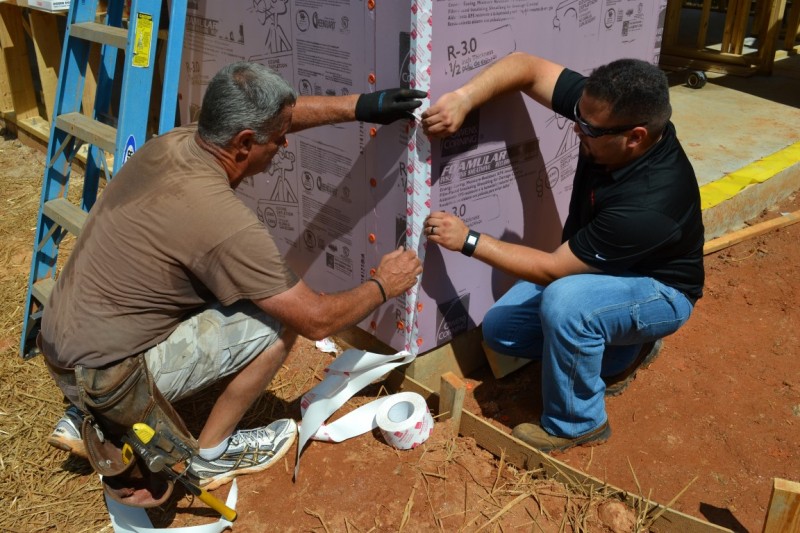
Another opportunity that we could NOT miss, or mess up, was preparing the sill, to get ready for the framing of the home, which took the framing crew a day-and-a-half. Normally, after that amount of time, they would have had most of the first floor framed up.
First, they secured the vapor barrier to the top of the slab-on-grade foundation, with liquid applied mastic. Next, they installed a continuous EPDM gasket, on top of the vapor barrier. So, why go through all this, as opposed to a standard sill sealer? To provide maximum control of moisture, through capillary action, and air, as a result of pressure changes, in and out of the house. These steps and the materials used provide a more durable and effective result.
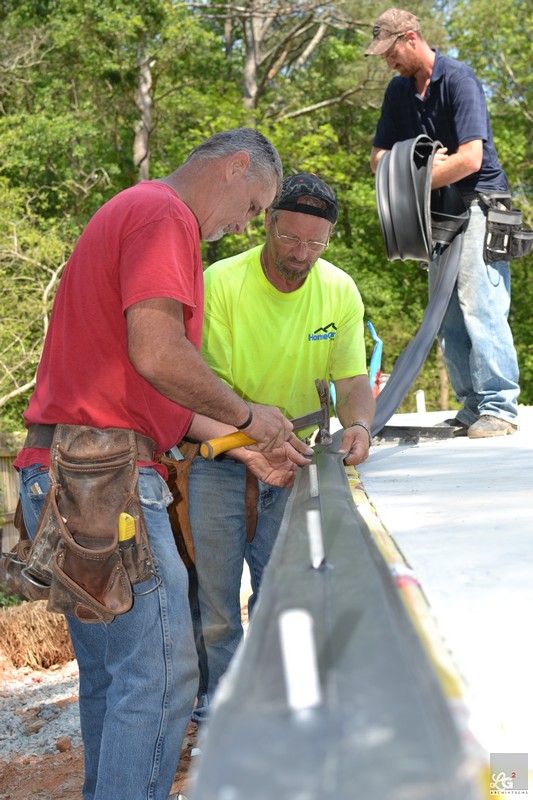
Building Science also says that for the entire building enclosure to perform properly, the insulation layer, air barrier layer, moisture barrier, and vapor barrier, MUST NOT be interrupted. Every corner, every penetration, every connection, all had to designed for this, but more importantly, the details had to be executed perfectly. Everyone on the job site had to know, and follow this. No exceptions. One mistake, or one missed detail, could cause failure in the building.
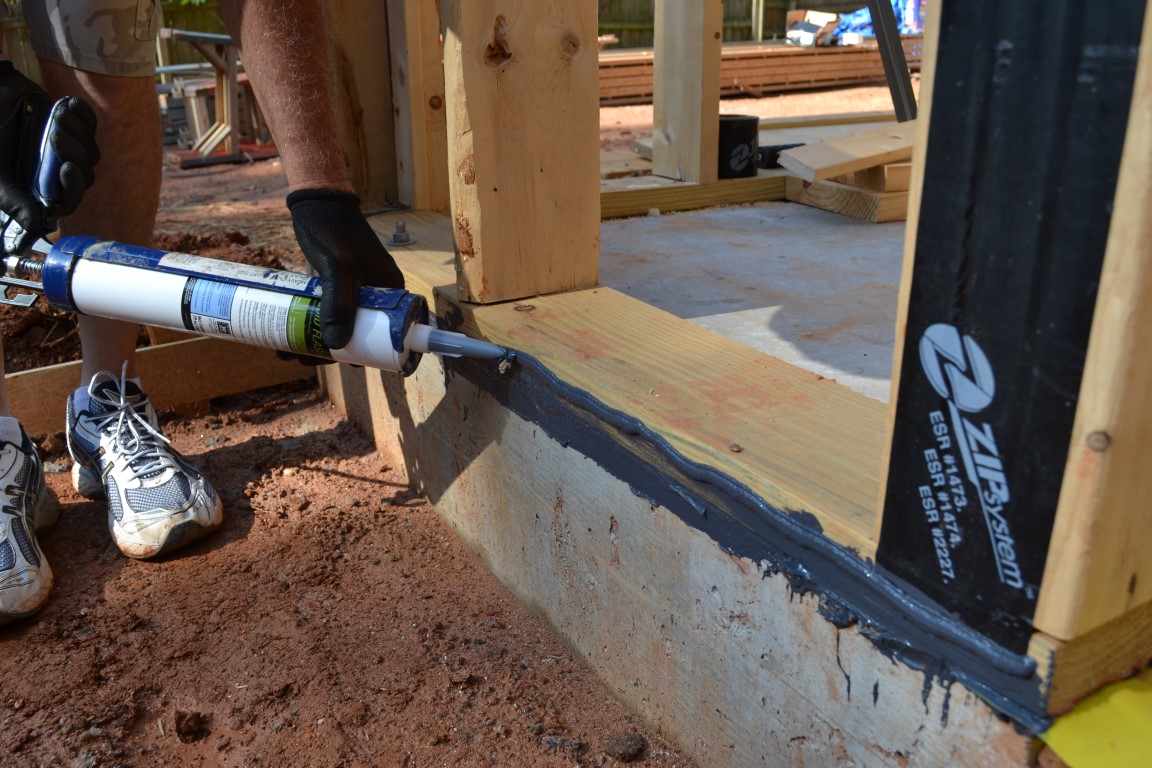
It's nothing new.
Just about everything, during the construction of the High Performance Bungalow, took a little to a lot more time than usual. That's what it takes.
Nothing we are doing is "new", just "right". Sometimes, we use a different material or approach. But, like any other home, there are walls, a roof and floors. To stay warm or cool, there is a heating and cooling system. The windows and doors are not custom fabricated, with three layers of a gel imported from Jupiter. And, the house is not insulated with hemp, mushrooms, or dirt. Teaser: You just might see a house insulated with hempcrete on this blog, someday soon...
CONFESSION: There is one thing we're doing different than most homes. Installing solar power. Over 6 kW of photovoltaic (PV) panels will be installed on the roof, which, based on the projections done by us and several third parties will, technically, make this a net-zero, maybe even a net-positive home. Only the monitoring equipment (which is also something not seen in most homes. OK, that's two things) that we've installed will tell us, for sure, after the home has been occupied for at least a year. We will share that data, here on the blog.
Just like the net-positive home we did in Serenbe, that has more energy production than consumption (net-positive), and is one of the tightest houses, anywhere, with an infiltration rate of 0.2 ach50, it doesn't look weird, or, frankly, like anything "high performance". It's just a house.
Proof is Possible
To verify that taking time is worth it, we perform diagnostic tests, early and often, and install monitoring equipment that will tell us how the house is performing for years to come. To quote our good friend, Corbett Lunsford, of the Building Performance Workshop, "Proof Is Possible". It's also necessary!
This is Abe Kruker, of SK Collaborative. He and his business partner, Carl Seville, are helping us "prove" how well we executed the science. They are the third party team verifying the performance through a series of diagnostic tests and visual inspections throughout the construction process.
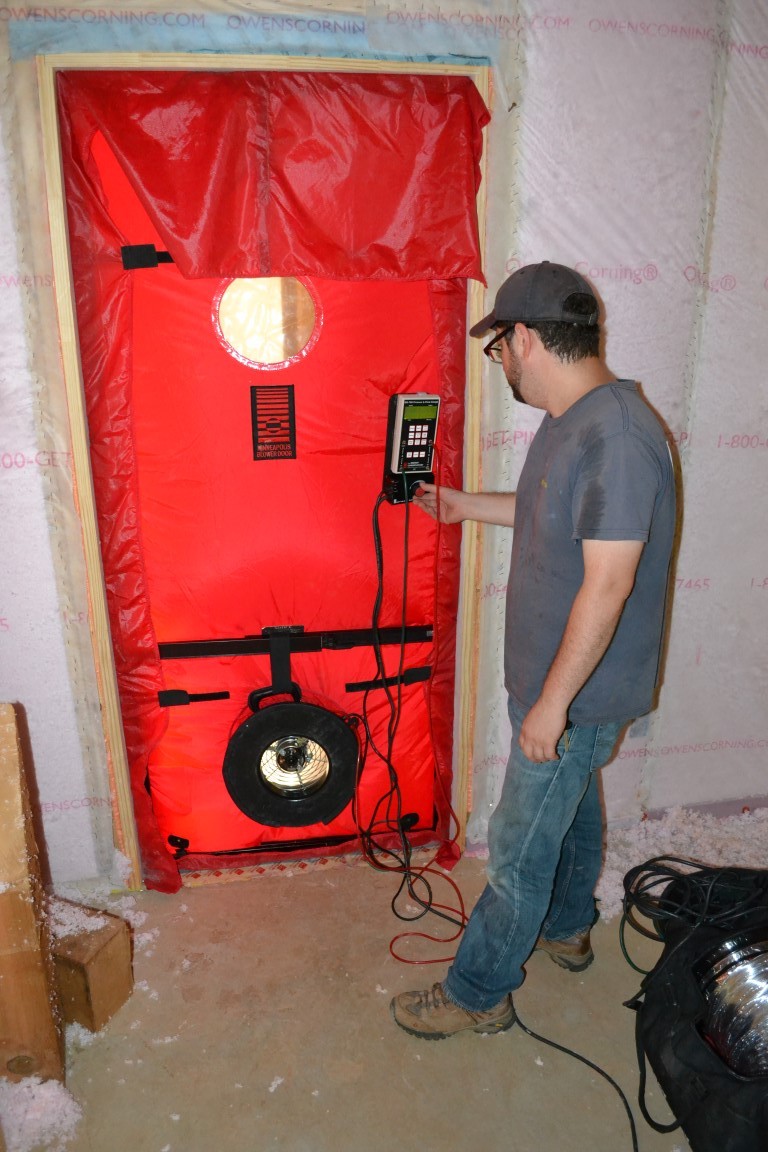
Here, Abe is using a duct tester fan, normally used to test duct systems, to test the the infiltration level of the home after the insulation was installed in the walls. We also performed a test before the insulation was installed, and we found that there was very close to the same amount of leakage. This tells us that the majority of the air is being controlled (stopped) on the outside of the building enclosure, where the science says it should be. This proves that the two layers of continuous insulation, the windows and doors, and utility penetrations, to name a few, were all well executed, no, done right!
The infiltration rate of the building enclosure on this home, before drywall, was measured at 0.98 ach50 (air changes per hour at 50 Pascals of pressure) before insulation, and approximately 0.95 ach50 after insulation. This is 86% less than maximum allowed by the 2009 International Energy Conservation Code (current in Georgia), which is 7.0 ach50, at final testing, just before occupancy.
During each test, with the help of a mini fog machine, and several folks walking around, looking for leaks, we found most of the remaining leakage is through the plumbing penetrations in the slab. This week, I'm taking the opportunity, with tubes of goo (liquid flashing) and spatuala in hand, to remedy that. I'm going to get the air under control. (It's also great for controlling termites!) What will the final results be?!?!
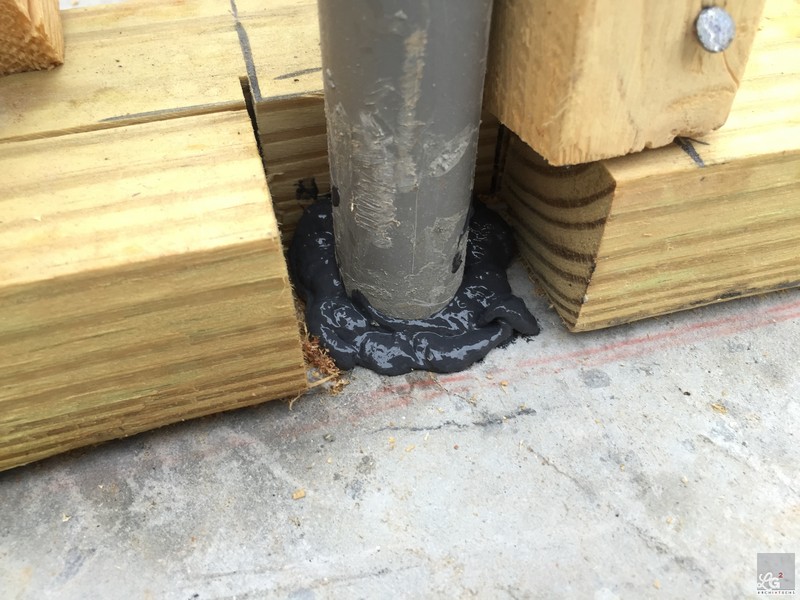
We're in to our seventh month of construction of the 2,600 square feet, 3 bedroom, 3 bath bungalow, and we're nearly finished. Cabinetry will go in this week, then tile, then polishing the concrete floors. Taking the opportunity to do things right has always proven to pay off, but you have to know it, first. Then, execute it. Period.
Follow along:
The High Performance Bungalow has it's own Facebook Page that's following the progress: facebook.com/HighPerformanceBungalow
...